1 Structural Defects of the Recycling System The plastic recycling industry faces a dual dilemma of “economic viability” and “ecological benefits”.
According to the Concepts and Practices of Plastic Pollution Control in China report, in 2021, the amount of waste plastic recycled into materials in China was only 19 million tons, with a recycling rate of less than 30%. Behind this data lie three major contradictions:
• High Sorting Costs: Sorting mixed plastic waste requires a large amount of manual labor. The sorting cost per ton of recycled plastic is as high as 800 – 1200 yuan, while the market price of recycled plastic is only 4000 – 6000 yuan per ton.
• Technical Bottlenecks: Mechanical recycling leads to a decline in material performance. For example, the strength of recycled PE material decreases by 30%. Although chemical recycling can preserve performance, the treatment cost per ton exceeds 15,000 yuan, and it also generates chlorine – containing wastewater.
• Imbalance between Supply and Demand: In 2023, the global demand for recycled plastics was about 120 million tons, while the actual supply was less than 40 million tons. A large amount of recycled plastics are forced to be used in a downgraded manner or cause secondary pollution due to substandard quality.
2 Hidden Costs of Energy and Environment The recycling process itself is becoming a new source of pollution: • Energy Consumption Black Hole: Producing 1 ton of recycled PET requires 3.5 tons of steam and 2000 kWh of electricity, with an energy consumption equivalent to 80% of that for producing virgin plastics.
• Chemical Pollution: During the recycling of electronic waste, 1.2 kilograms of polychlorinated biphenyls (PCBs) are released per ton of waste plastic, far exceeding the EU emission standards.
• Carbon Emission Paradox: The global plastic recycling industry emits 120 million tons of CO₂ annually, equivalent to the annual emissions of 30 million cars.
3 The Vicious Cycle of Incineration and Landfill When recycling fails, the final destination of plastic waste is often incineration or landfill:
• Carcinogenic Chain of Incineration: Burning 1 ton of plastic releases 3 grams of dioxins, which are 900 times more toxic than arsenic. The risk of lung cancer increases by 30% in long – term exposed populations.
• Landfill Crisis: The Plainfield Landfill in the United States, the world’s largest plastic landfill, leaks plasticizers into the surrounding groundwater every year, causing a 17% increase in the incidence of precocious puberty among children within a 10 – kilometer radius.
The Ecological Revolution of Biobased Degradable Materials
The Life Cycle from Plants to Materials The production process of biobased materials reconstructs the relationship between humans and nature:
• Raw Material Innovation: Polylactic acid (PLA) uses corn starch as raw material. Every ton of PLA can consume 2.5 tons of corn, equivalent to absorbing 3.2 tons of CO₂.
• Fermentation Process: The PHA production technology developed by the Chinese Academy of Sciences uses kitchen waste for fermentation, reducing CO₂ emissions by 4.5 tons per ton of PHA.
• Energy Efficiency: The production energy consumption of biobased materials is 40% lower than that of traditional plastics. For example, the energy consumption of producing polyhydroxyalkanoates (PHA) is only 60% of that of polypropylene.
Ecological Friendliness of the Degradation Process Different from the “permanent” characteristics of traditional plastics, biobased materials achieve material circulation:
• Complete Degradation: PLA decomposes into CO₂ and water within 60 days under industrial composting conditions, while traditional PE takes more than 200 years.
• Soil Improvement: Research by Tsinghua University shows that after the degradation of biobased agricultural films, the soil organic matter content can increase by 12%, and the earthworm density can increase by 200%.
• Marine Adaptability: The biobased polyurethane foam developed by the University of California begins to degrade within 4 weeks in seawater and completely disappears after 16 weeks.
Double Breakthroughs in Performance and Cost Biobased materials are breaking through the misconception that “environmental protection = low performance”:
• Performance Benchmarking: The heat resistance of polybutylene succinate (PBS) reaches 110°C, which can replace PP for microwave – safe food containers. The oxygen barrier property of polyethylene furanoate (PEF) is three times that of PET.
• Cost Reduction: The production cost of PEF by YOUHUA New Materials is 20% lower than that of PET. After large – scale production, the price gap will be reduced to less than 5%.
• Capacity Expansion: China’s biobased material production capacity will reach 4.59 million tons in 2025, with PLA production capacity accounting for 60% of the global total.
Industrial Breakthrough: From the Laboratory to the Market
Diversified Expansion of Application Scenarios Biobased materials are reshaping multiple industries:
• Packaging Field: Starbucks stores in the United States have switched to PLA – lined paper cups, reducing the use of 1 billion plastic cups annually. The French cognac brand Angély has launched bottles made entirely of PLA, reducing the carbon footprint by 80%.
• Medical Field: The biobased nanomaterials developed by Nanjing Forestry University have increased the targeting efficiency of anti – cancer drugs by 10 times. The wooden 3D – printed bone nails developed by Zhejiang A&F University have passed animal experiments, with biocompatibility superior to titanium alloy.
• Agricultural Field: The biobased agricultural films promoted in Huizhou have increased potato yields by 15% per mu while reducing 15 kilograms of plastic residues.
Key Breakthroughs in Technological Innovation • Revolution of Non – Grain Raw Materials:
The PEF materials developed by YOUHUA use agricultural waste as raw materials and have successfully completed ton – scale trial production. East China University of Science and Technology has developed biobased luminescent materials using γ – cyclodextrin, achieving “zero – waste” production.
• Upgrades in Degradation Technology: The PBAT/PLA blend developed by Professor Jiang Hui’s team reduces the microplastic risk by 90% while ensuring performance.
• Empowerment by Digital Technology: The blockchain platform of Alibaba Cloud realizes the whole – process traceability of PLA products from farmland to shelves, ensuring the authenticity of the biobased content. 4.3 The Industrial Logic of Cost Reduction The cost disadvantage of biobased materials is being eliminated by large – scale production:
• Economies of Scale: The global production capacity of PLA will reach 3.8 million tons in 2025, and the unit cost will drop to 12,000 yuan per ton, approaching the price of PP
. • Technological Iteration: The biobased polyamide developed by China Merchants Group has reduced the production cost by 40% through AI – optimized strains.
• Policy Support: The EU’s “Microplastic Restriction Bill” requires 30% of petrochemical plastics to be replaced by 2030. China’s “Plastic – Banning Order” has increased the penetration rate of degradable plastics from 0.6% in 2020 to 15% in 2025.
Existing Challenges and Solutions
1 Shortcomings of Degradation Facilities Industrial composting facilities globally only cover 20% of the population. China plans to build 500 regional processing centers by 2025. Research by Tsinghua University shows that if biobased materials do not enter the composting system, their landfill carbon emissions will be 5 times higher than those of traditional plastics.
2 Gaps in Cognition and Standards Consumers generally misunderstand that “degradable” means “can be discarded at will”, so more efforts are needed to strengthen label management. The EU requires that all biobased products be labeled with degradation conditions by 2025. China has issued the Measures for the Identification and Traceability Management of Biobased Materials, promoting the standardization of the industry.
3 Improvement of Technical Standards Establish a unified detection method for biobased content. For example, the near – infrared spectroscopy method developed by Tsinghua University can complete the detection within 30 seconds. At the same time, the lack of marine degradation standards needs to be addressed. Tianjin University has discovered that the bacterium Exiguobacterium marinum a – 1 can degrade polypropylene, providing a new path for marine plastic treatment.
Future Prospect: Material Revolution and Civilization Transformation
Frontier Explorations in Materials Science • Gene – Edited Crops: The development of salt – and alkali – tolerant PHA – producing plants has been successful, breaking through the raw material bottleneck.
• Bioinspired Materials: Biobased composite materials mimicking the structure of shells have increased strength by 300%.
• Self – Healing Materials: The biobased polyurethane developed by Zhejiang University can automatically repair scratches within 24 hours.
Construction of a Closed – loop Circular Economy
• Closed – loop Production: The Dutch company Heuritech converts biobased material waste into new materials, achieving “zero waste”.
• Digital Twin: The digital twin system of biobased materials constructed by Haier Group reduces energy consumption by 25%.
• Carbon Sink Trading: The carbon sink value of biobased materials has been incorporated into the national carbon market, and each ton of PLA can be traded for 1200 yuan.
Reconstruction of the Civilization Paradigm When the degradation cycle of biobased materials is synchronized with the rhythm of the natural ecosystem, humanity will complete the transition from “conquering nature” to “symbiotic evolution”.
As stated in the 12th Five – Year Special Plan for the Scientific and Technological Development of the Biobased Materials Industry, this is not just a material substitution but a redefinition of the relationship between humans and the Earth.
Conclusion: Rebirth in Degradation The rise of biobased degradable materials marks the beginning of humanity’s reconstruction of industrial civilization using the logic of life science. When PLA lunch boxes turn into spring mud in the soil, when PHA agricultural films nourish the black soil, and when polyurethane foam in the ocean becomes a feast for microorganisms, we are writing a new natural history – not plastics conquering the earth, but life reshaping civilization. The ultimate significance of this revolution lies in proving that technological innovation can resonate with ecological ethics, and human wisdom can coexist harmoniously with the laws of nature.
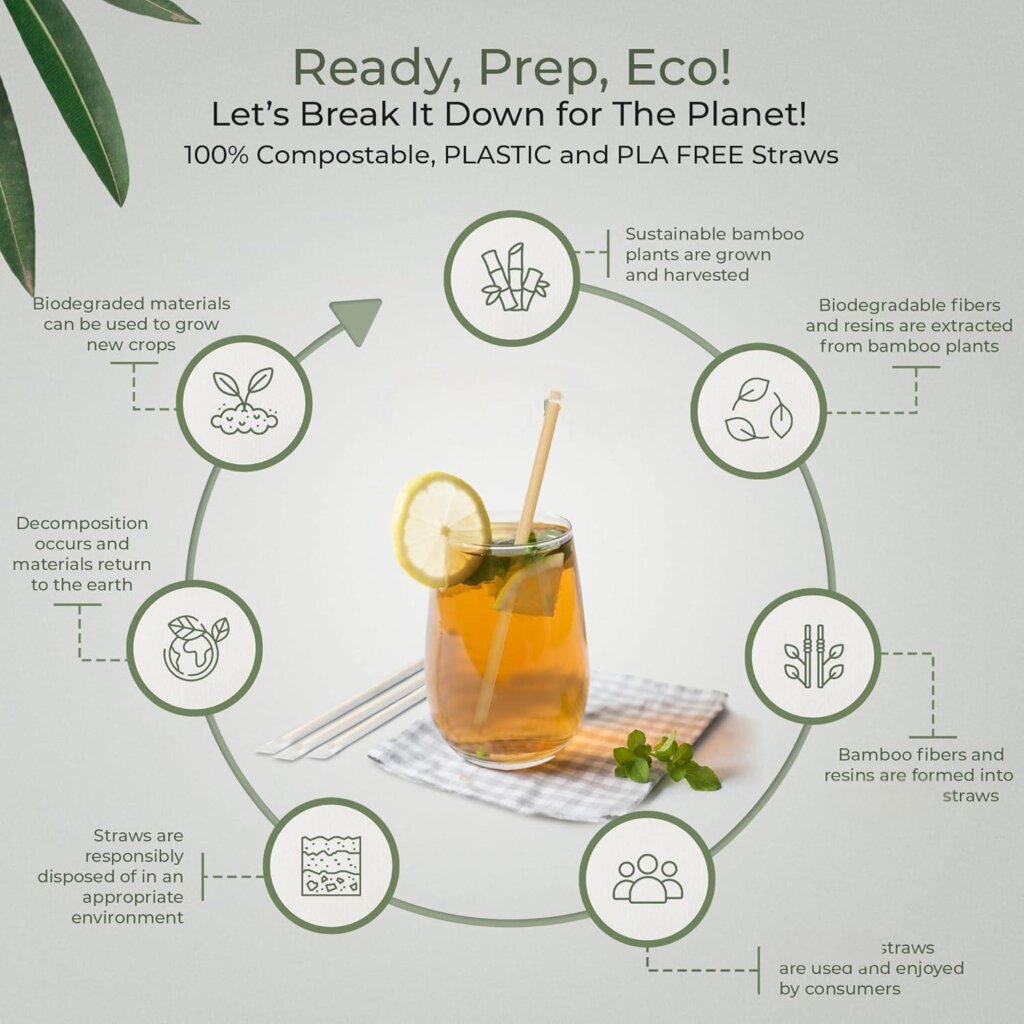